The costs associated with technical compliance is one of the items that should be considered in the budget of all product development projects. Unfortunately I have observed in many projects that this item is not considered, or is considered incompletely.
We can define technical compliance as the activity of “comply with the requirements (regulations and legislation) and with the compromises (volunteers o self-imposed) of a organization, related with the technique and technology”. If, as a consequence of not having budgeted for technical conformity, the worrying situation arises that you have not ensured that a new product or a modified product meets the requirements and commitments that it should; we can put the company at risk of being denounced for failing to comply with the legislation or for infringing industrial property rights.
Therefore, to avoid uncomfortable situations in our company (or venture) we must incorporate a sheet related to technical conformity into the project budget for a new (or modified) product.
Let's see with an example the concepts that we should take into account. Suppose we want to develop a new line of products connected to the low-voltage electrical network, which, depending on the version, will incorporate wireless communication components, and that we want to market in the European Union market.
Given this environment, we must consider compliance with community legislation and compliance with the technological standards used.
- Compliance with community legislation (CE marking).
In this area, given the type of product, the main directives and regulations to consider are:
- Directive 94/62/EC on packaging and packaging waste (Packaging).
- Directive 2009/125/EC establishing ecodesign requirements applicable to energy-related products (ErP).
- Directive 2011/65/EU on restrictions on the use of certain hazardous substances in electrical and electronic equipment (RoHS).
- Directive 2012/19/EU on waste electrical and electronic equipment (WEEE)
- Directive 2014/30/UE regarding electromagnetic compatibility (CEM).
- Directive 2014/35/EU on the sale of electrical equipment intended for use with certain voltage limits (Low Voltage).
- Directive 2014/53/EU on the marketing of radioelectric equipment (RED).
- Regulation (EU) 2017/1369, of July 4, 2017, establishing a framework for energy labelling.
If a piece of equipment has moving parts, the application of the "Directive 2006/42/EC relative to machines" should be considered.
The costs that we should consider are those of regulations, advice and tests.
- The costs of acquiring regulations.
As explained in the previous article, a strategy to ensure that our product meets the requirements described in the different directives and achieve the presumption of conformity, the most advisable thing is to use the harmonized standards published in the Official Journal of the European Union ( DOUE) for each of the directives (and that are applicable to our product). Therefore we have to consider the cost of harmonized standards for each of the directives and regulations:
For the Packaging Directive, the harmonized application standards go from EN 13427 to EN 13432, its cost is 332 euros.
For the ErP Directive, we must take into account that the products to which it applies must have been subject to an implementing measure, which is usually a regulation that defines the ecodesign requirements that apply to a group of products. . As of the date of this article, there were 27 ecodesign regulations. For example, for domestic dishwashers, Regulation 1016/2010 applies, which has EN 50242 as a harmonized standard (105 euros). However, it must be taken into account that for domestic dishwashers as of March 1, 2021, Regulation 2019/2022 comes into effect. Therefore, as of that date, any domestic dishwasher that is sold must comply with the provisions of the new regulation.
For the RoHs directive, the harmonized application standards (which will help us understand how to document our project, which are the tests to be carried out and how to interpret the results) are EN 50581, EN 62474 and the EN 62321 series. For all of them we have to foresee a budget of 1.160 euros.
For the WEEE Directive there are no harmonized standards.
For the EMC directive in the last update of November 2020 there are 264 harmonized application standards. Of these, the most used as basic standards, which are used for the majority of electrical and electronic products, are part of the EN 61000 series, with a cost of 1.044 euros. In addition, depending on the group of products, other harmonized standards could also apply. Thus, for example, for household appliances, the EN 55014 series (210 euros) would apply.
For the Low Voltage directive, the harmonized application standards are those of the EN 60335 series. The basic ones are the 60335-1 subseries with a budget of 407 euros, and the specific ones for each group of products are those of the 60335-2 subseries ( it will be necessary to determine which of the 111 standards of this subseries describes the particular requirements of our product).
For the RED directive in the harmonized application standards there is no basic one, the standards to be applied will depend on the radioelectric or geolocation modules that we install. And depending on this, if the EN standards to be applied have been developed by CENELEC we will have a cost, but if they have been developed by ETSI then they are free.
For the Energy Labeling Regulation, the harmonized application standards will be linked to the Delegated Act of the Commission that has been published for a certain group of products. It will only apply to products for which a Delegated Act has been published. Thus, for example, we have that Delegated Regulation (EU) 2010/1059 was published in 2010 for domestic dishwashers, for which it was later published in the DOUE that the harmonized application standards were EN 50242 (with a cost of 105 euro).
We will only have the cost of the standards for the first product project (or if we have several we will divide the budget among them). But for future projects we must remember that "Execution Decisions of the Commission" are periodically published in which the modifications in the lists of harmonized standards are determined. And if new application standards appear, we must acquire them. And depending on the date on which these modifications enter into force, the products that we market as of that date must comply with the regulations of those modifications. By way of example, on October 27, 2020, an Execution Decision was published for the RED Directive incorporating the EN 301 908-2 V13.1.1 standard, which from that date was the one that the products to which it referred and that were sold had to comply from that date.
- Consulting costs that help us meet essential requirements.
In order for our product to obtain the presumption of conformity with the essential requirements established in the legislation, we must apply the indications of the harmonized standards that apply to it in its design, development and manufacture; and we must pass the tests described in these standards. To achieve this, we must have expert personnel in the company in compliance with each of the laws, or subcontract experts who help us in whole or in part. Of the aforementioned directives, the one that normally presents the greatest complexity when it comes to passing the tests is that of Electromagnetic Compatibility (EMC).
When budgeting for this external support, there are different strategies for action. The most economical is to do nothing and take our product to be tested with what our technicians have developed. The usual thing in this case is that a percentage of around 50% of the products do not pass the CEM tests. If we consider that our technicians do not have sufficient knowledge and experience in electromagnetic compatibility, we can hire an expert from the beginning of the project to help us define the best arrangement of components and technological solutions for our product, and to advise us on everything. the process until the tests that give us the conformity of the product are passed. This option has a minimum cost of 4.000 euros, which will increase depending on the complexity of the product.
Another option is to develop a non-definitive functional prototype of the product on our own and carry out investigative tests in a laboratory that has the appropriate instruments. In this case, the cost of the tests is between 150 and 200 euros/hour (we will need at least four hours for the usual tests).
In these tests it is advisable to take several prototypes that have different technological solutions or components to see how they behave. If no prototype works for us in these tests, then it is advisable to hire an expert, because surely that way we will not pass the final tests. If we have passed these investigative tests, then we will develop the production prototypes, that is, the prototype of the product that will be final and that we will take to production without modifications after the final tests. Before taking these definitive tests to this "production prototype" it is advisable to carry out some pre-evaluation tests to verify that the main tests of the regulations are met (this test has a cost of around 1.000 euros).
- The costs of testing the directives in an accredited laboratory.
In most companies (and especially entrepreneurs) the instruments and infrastructures are not available to be able to test the products in accordance with what is described in the harmonized standards. For this reason, a laboratory is usually subcontracted to carry out the tests to verify that the product complies with the harmonized standards and therefore we can give a presumption of conformity for those directives.
For the RoHs directive, the budget to be considered in the tests is a minimum of 500 euros.
For the CEM directive we must consider a minimum budget of 2.000 euros.
For the Low Voltage directive we must consider a minimum of 2.000 euros.
For the NETWORK directive we must take into account that among its essential requirements is to guarantee compliance with the Low Voltage directive without applying the voltage limits and guarantee compliance with the EMC directive. Therefore, the tests for the NETWORK Directive include the tests of the NETWORK, the EMC tests and the Low Voltage tests. For this directive, the most economical test, which would be, for example, that of a device powered by a battery and that includes a RED certified module, the budget would be between 7.000 and 8.000 euros (taking into account the fact of incorporating RED certified modules reduces the cost of trials).
For the products that are intended to be marketed for the IoT, the test costs would be between 8.000 and 9.000 euros. If we have a device with a Bluetooth module and 2,4 GHz Wi-Fi powered by a 220 Vac network connection, the cost of the NETWORK tests is of the order of 15.000 euros. When cellular technologies such as LTE are used, costs increase substantially because multiband studies are required. If we use cellular technology modules in our products, the costs will increase even more because it requires specific tests for these technologies.
We must bear in mind that this cost will increase if there are breaches in any of the tests defined by the regulations and after modifying the "production prototype" we must redo them completely with the subsequent extra cost. Here, a strategy to take into account is that if some non-compliance occurs when the tests are being carried out (we do not pass a test), the reasonable thing to do is to finish the tests to redesign our product and manufacture a new prototype; paying only for what is done.
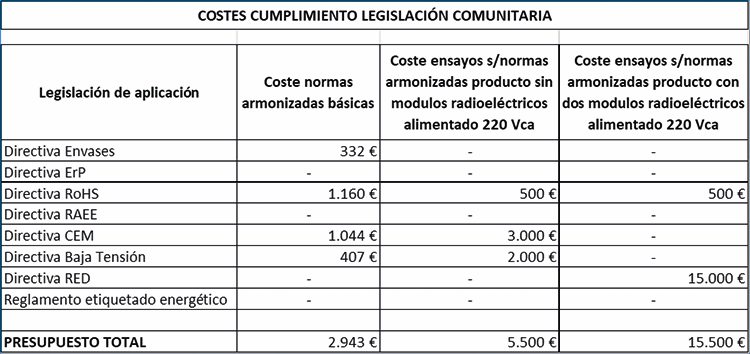
Figure 1. Costs to consider in the budget for CE marking compliance.
- Compliance with technological standards.
Most of the technologies used today in electrical and electronic products are related to technological standards, with wireless communications and cellular technologies being one of the areas with the highest incidence of associated costs. If it happens that we use components that use these technologies, we should budget the cost of the license to use these technologies and the tests to validate that they comply with those standards.
Let's see as an example the case in which we decided to incorporate a Bluetooth module into our product.
- The costs of the licenses for the use of technological standards.
If we want to market a product with a Bluetooth module, and in which we want to have the Bluetooth® logo, we must know that the product must be "qualified" on the date it begins to be sold or distributed (or better before that date). ). The product qualification process is defined by the Bluetooth SIG, which is the organization that certifies and registers products that can legally bear the Bluetooth logo and comply with the Bluetooth standard.
In this section of the budget we must consider the cost of obtaining the qualification of the product that will allow us to commercialize without problems with Bluetooth SIG. This requires you to pay the Declaration cost, which must be done for any new, modified, used or Bluetooth-branded Bluetooth products. For this Declaration there are two options: on the one hand we have the route of the so-called Associate Member which has an annual fee of 7.500 dollars for companies with a turnover of less than 100 million dollars per year, to which is added the cost of the Declaration of product that is $4.000. On the other hand, if we consider the Adopter Member route, there is no annual fee for the company, but in this case the cost of the Statement is $8.000.
- Laboratory costs to validate compliance with technological standards.
At this point we have to consider the cost budget to certify our product in the technology (or technologies) that we have incorporated. In the case of Bluetooth, we have to validate our product in one of the laboratories accredited by Bluetooth SIG, which has a minimum cost of 6.000 euros. Here it must be taken into account that not all products that incorporate a Bluetooth module must be validated by an accredited laboratory. To do this, we must see what is the qualification route of our product that is established by means of the Bluetooth SIG qualification tool called Launch Studio. If this tool determines that our product should not go through the laboratory, we will not have this cost.
If in our product we have other communications modules such as Wifi, LoRa, 5G or others, we must budget their corresponding compliance costs, which will be the sum of the costs for the license to use the technology and for compliance of the product with the standard.
Figure 2. Costs to consider in the budget for compliance with technological standards.
- Other costs in compliance with community legislation.
- The costs of preparing the technical documentation.
Community legislation establishes that products bearing the CE marking must have technical documentation that provides information on the design, manufacture and operation of the product and that demonstrates the conformity of the product with the applicable requirements. A documentation that will be available at a potential request from the market surveillance authorities, and that must be kept for ten years from the date of sale of the unit corresponding to that documentation. Important to remember "since marketing"; If we manufacture a product and it remains in our warehouse for, for example, four years, we must keep the documentation for fourteen years from the date of manufacture (4 years +10 years).
For the elaboration of the technical documentation, we must take into account the cost of the internal personnel that must carry it out and, if we do not have sufficient knowledge of the requirements of this documentation, the subcontracting of experts in the subject.
- The costs of marketing on the Community market.
A directive whose costs have not appeared is the WEEE Directive. This directive affects the sale of electrical and electronic products because it is the directive that generates the cost associated with the recycling of electrical and electronic products.
The first procedure to carry out is the registration in the special section for producers of electrical and electronic equipment of the Integrated Industrial Registry.
And we have to decide if we choose to establish our own individual system of "extended producer responsibility" with which we must manage the collection of waste from our products and assume the costs associated with that management. Or, the best option for most companies, to subcontract a collective system through a SCRAP (Collective System of Extended Producer Responsibility). Of the products that this directive applies, transposed in Spain by Royal Decree 110/2015, we must provide quarterly information on its commercialization. In addition, we must provide the documentation that allows its optimal recycling (or its repair). Each unit that we sell of a product will have a rate that will be determined by the SCRAP and that will be different for each type of product.
At the beginning of the article, I stated that we wanted to develop a new line of products connected to the low-voltage electrical network, which, depending on the version, would incorporate wireless communication components (a Bluetooth certified module), and that we wanted to market in the European Union market. . In this case, the budget that we must consider for technical compliance before marketing is 26.443 euros.
This is an assumption that is not considered on too many occasions, which causes the different compliance procedures to not be carried out, and which can have serious consequences such as: complaints for infringement of industrial property on technological standards, or environmental complaints for marketing products with dangerous substances, or reports of smuggling of prohibited substances if these products are exported, or reports on security issues due to electromagnetic interference with facilities or with other products.
In conclusion, my recommendation is that: if a company (or entrepreneur) wants to develop a new electrical-electronic product, it must take into account in the project budget the costs derived from compliance with technical compliance.
References:
- Directive 94/62/CE, relative to packaging and packaging waste
- Directive 2009/125/EC, establishment of ecodesign requirements applicable to energy-related products
- Directive 2011/65/EU, on restrictions on the use of certain dangerous substances in electrical and electronic equipment
- Directive 2012/19/EU, on waste electrical and electronic equipment (WEEE)
- Directive 2014/30/EU, on the harmonization of electromagnetic compatibility
- Directive 2014/35/EU, on the harmonization of the marketing of electrical equipment intended for use with certain voltage limits
- Directive 2014/53/UE, relative to the harmonization on the commercialization of radioelectric equipment
- Regulation (EU) 2017/1369, of July 4, 2017, establishing a framework for energy labeling
- Royal Decree 110/2015, of February 20, on waste electrical and electronic equipment.
- Bluetooth SIG (https://www.bluetooth.com/)